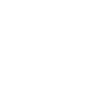
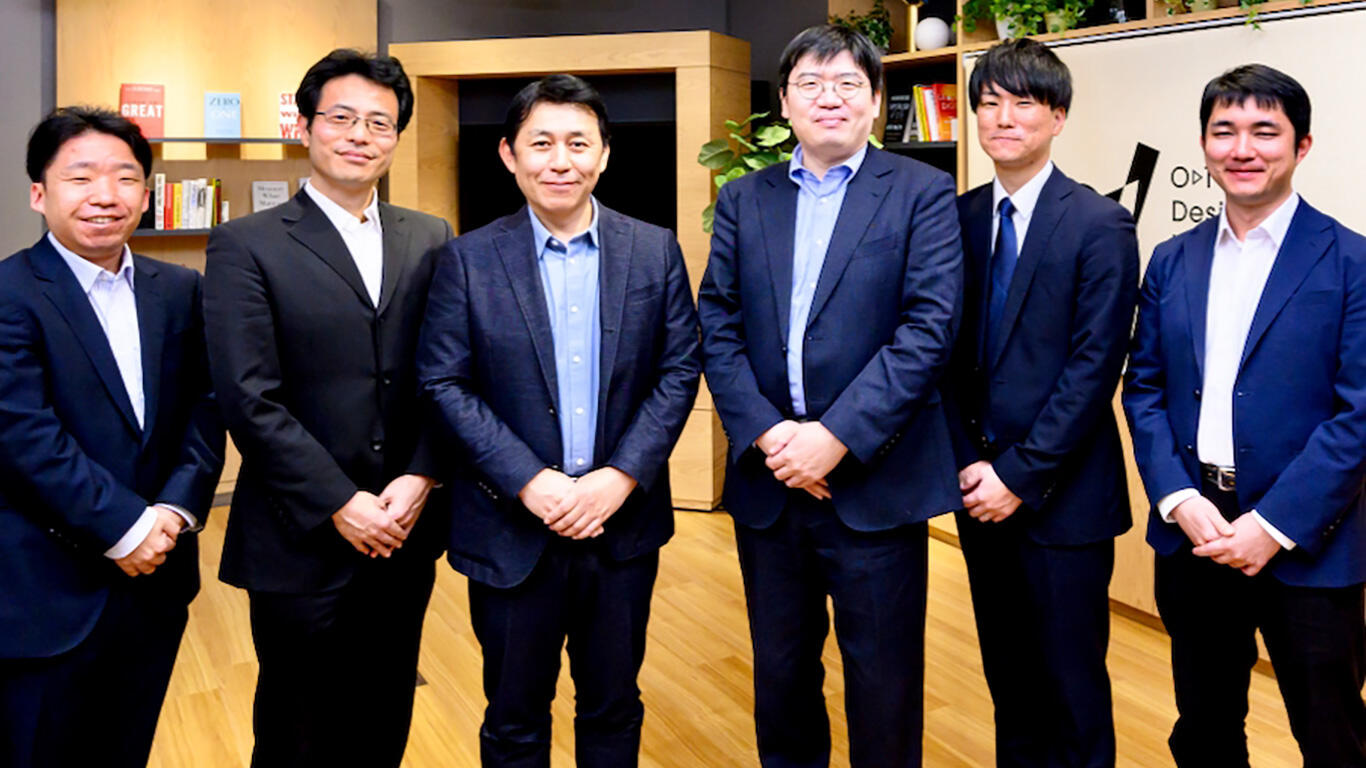
進化する最適化技術VOL.3
~製鉄所の生産計画立案を変革、日本製鉄×NSSOLが挑む熟練者業務のDX数理最適化技術で製鋼工程の生産計画を数分で立案可能に~
日本製鉄は、同社生産の要となる製鋼工程の生産計画を立案する「出鋼スケジューリングシステム」を日鉄ソリューションズ(NSSOL)と共同で開発し本格運用を始めている。熟練技術者が約8時間かけていた計画を、計算機がわずか数分で立案する。確認・調整などの作業を含めても、トータルで70%の時短を達成し、計画のレベルも同等以上だ。数理最適化技術を活用し、熟練技術者の暗黙知をアルゴリズムに落とし込んだ。製鋼工程を対象にしたシステム整備の狙いや開発時の苦労、今後への期待などをプロジェクト担当者が語った。(本文敬称略)
――日本製鉄の東日本製鉄所 君津地区では、製鋼工程の生産計画を立案する「出鋼スケジューリングシステム」を稼働させています。製鉄における「製鋼」とは、どのような工程でしょうか。
河井田 博昭(以下、河井田):日本製鉄 東日本製鉄所 工程業務部 工程企画室長の河井田 博昭です。製鋼は製鉄において“要”となる工程です。製鋼工程の生産計画が、その前後の工程における計画にも影響を与えます。
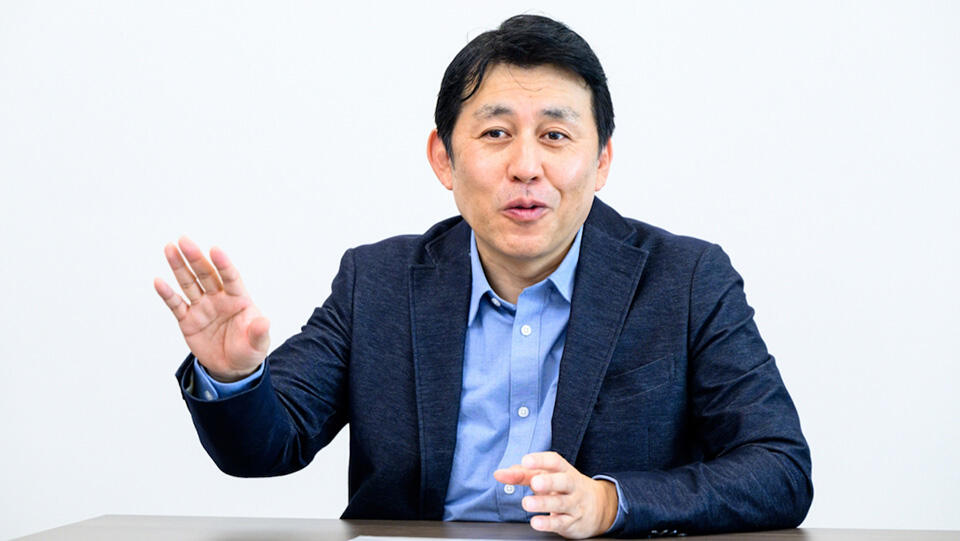
河井田:鉄の原材料は鉄鉱石と石炭を蒸し焼きにしたコークスです。これらを高炉の中で熱して溶かし「銑鉄(せんてつ)」を作ります。この銑鉄から不純物を分離したり、逆に必要な添加物を投入したりして成分を調整し、中間製品の「スラブ」を作る工程が製鋼です。このスラブを薄く延ばしたり表面処理を施したりしたものが当社の最終製品である薄板になります。
鉄は、炭素や他の金属などの含有物の量によって、硬さや、しなやかさなどの特性が変わります。例えば自動車用の鉄材にしても、車体の骨格には強度の高いものが、ボディー用には加工しやすく軽いものが求められます。それらの特性を決めているのが製鋼工程です。
現在当社では、さまざまな顧客ニーズに合わせ、特性が異なる2万種類以上の鉄鋼製品を受注生産しています。注文数は1週間で万単位です。つまり製鋼は、受注状況に合わせて製品の特性や品質を決定する重要な工程なのです。
10の300乗もある選択肢の中から最適な計画を立てる
河井田:しかし、スラブの生産計画を立てるには、さまざまな制約条件が存在するため一筋縄ではいきません。まず製鋼は、含有物質が同じになる「鍋」が1つの単位になり、君津地区の鍋は約300トンの大きさです。一方で当社の受注単位は10トン前後のため、複数顧客からの受注状況を見て、特性が同じものを選び出し、300トンになるよう組み合わせる必要があります。
加えて、作る順序も重要です。鍋の組合せや順序によっては、歩留が大きく低下します。注文の組合せ、鍋の組合せや順序の掛け合わせでその数は膨大になり、単純計算では10の300乗にもなります。2万種類の製品を、これらの制約条件の下で生産する計画をどう最適化するかは、歩留ロスのような無駄をどれほど最小にするかという課題でもあります。
枚田 優人(以下、枚田):日本製鉄 情報システム部 情報システム企画二室 AIソリューション課長の枚田 優人です。君津地区が受注生産している薄板の量は週に約10万トンです。それを上述したような生産上の制約や納期、さらには今後の受注見通しなども加味しつつ生産計画を立てるのです。
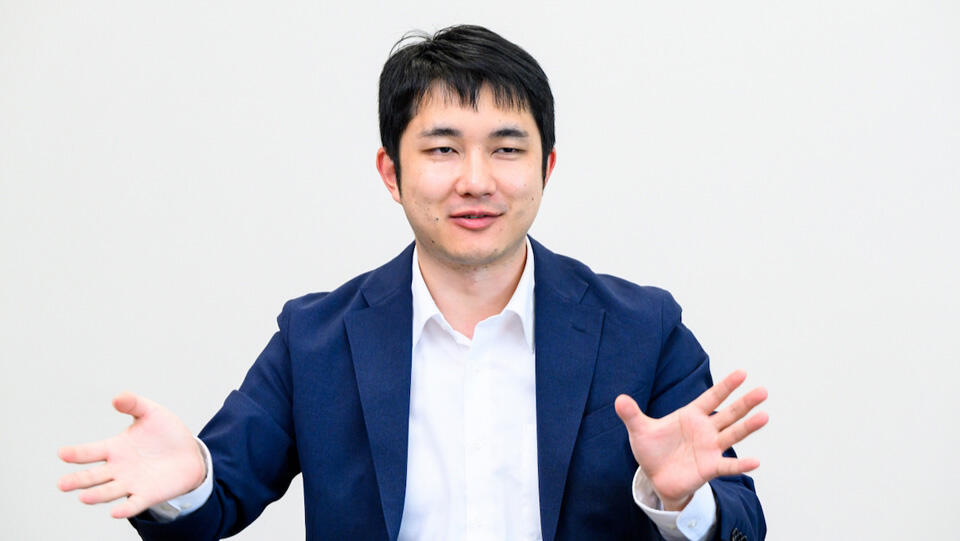
枚田:万一、計画が不適切だと品質を守れなかったり、最悪は納期に間に合わないといった事態が発生します。組合せによっては余剰生産を余儀なくされ、在庫も積み上がります。在庫は廃棄こそしないものの、次工程で圧延加工するためには、一度冷めてしまったスラブを1000度以上まで加熱せねばならずエネルギーロスも生じます。高温のまま、できるだけ連続して生産する理由は、ここにもあります。
こうした途方もない組合せがある選択肢から最適な生産計画を決める作業は、いわゆる組合せ最適化問題の一種です。これまでは、製鋼工程だけでなく、その前後の工程にも精通したベテラン技術者が、長年の経験で獲得した暗黙知を基に長時間かけて立案するしかありませんでした。この方法では受注動向や生産変動などへの迅速な対応が難しく、競争がグローバルで激化する中では、業務高度化の阻害要因にもなってきたのです。
生産の起点であり業務への影響も大きい課題をあえて選択
――それほど複雑な工程のシステム開発に踏み切った理由はなんでしょう。
河井田:生産計画の自動化自体は決して目新しいテーマではなく、20年以上前から研究に取り組んできました。今回、製鋼工程の自動化に取り組んだのは、ここが鉄鋼生産の要であり、前後の工程への影響も大きいだけに、業務改善策として最も大きなインパクトが見込めるためです。将来的な熟練工不足や人材育成の難しさといった課題に対応するという狙いもありました。
追い風になったのが、2020年に発表した中期経営計画においてDX(デジタルトランスフォーメーション)推進を経営目標に掲げたことです。同目標に沿って「デジタル改革推進部」が新設され、一方で深層学習や組合せ最適化など先進IT技術に対応する「インテリジェントアルゴリズム研究センター」が2018年に立ち上がりました。技術面に加え、経営判断として組織面でも推進体制が整ってきたのです。
森田 幾太郎(以下、森田):日本製鉄 デジタル改革推進部 主幹の森田 幾太郎です。ハードウェアとソフトウェアの急速な進化も見逃せません。組合せ最適化問題の最大の課題は、解を得るための演算処理時間です。従来は気が遠くなるほどの時間を要しましたが、近年は計算機の高速化や汎用ソフト・アルゴリズムの高度化が相まって、製鋼工程の生産計画のような複雑な問題でも、数理最適化モデルの工夫次第で処理時間が現実的に利用できるレベルにまで短縮されました。
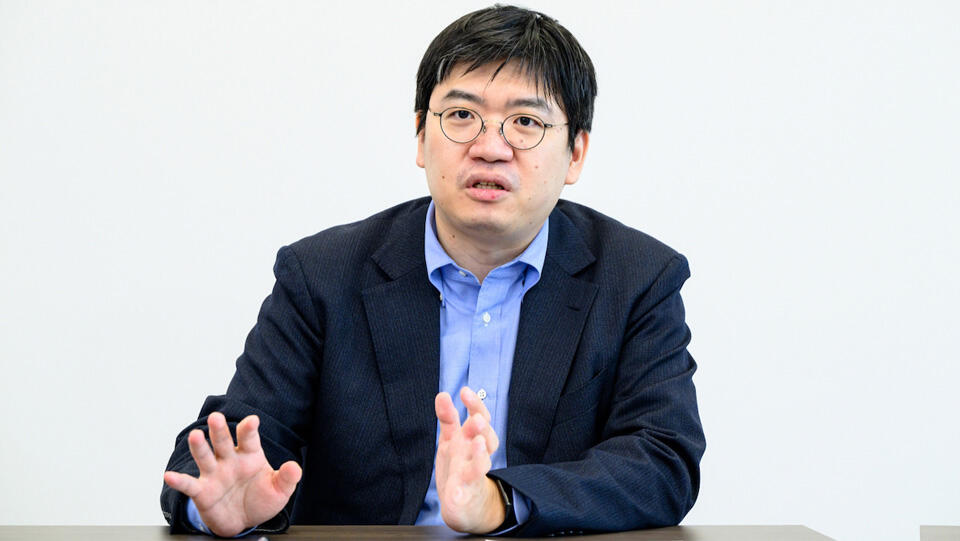
森田:これらがうまく噛み合った結果、DX戦略が掲げる「生産計画DX」の一環として出鋼スケジューリングシステムのプロトタイプを2021年2月に稼働させることができました。以来、人手による計画を併用しながらシステムの改善を繰り返し、2023年3月に本番稼働させました。
――システム化で最も苦労したのは、どういった点でしょうか。
山本 政(以下、山本):日鉄ソリューションズ(NSSOL)システム研究開発センターの山本 政です。一言で言えば、熟練技術者が持つ暗黙知のモデル化・定量化です。生産計画の策定時、熟練技術者はいくつもの観点から計画の良し悪しを判断していますが、それらは感覚も含めた属人的な知見です。その判断基準のすべてを人手で書き出して明文化することは実際問題として不可能です。
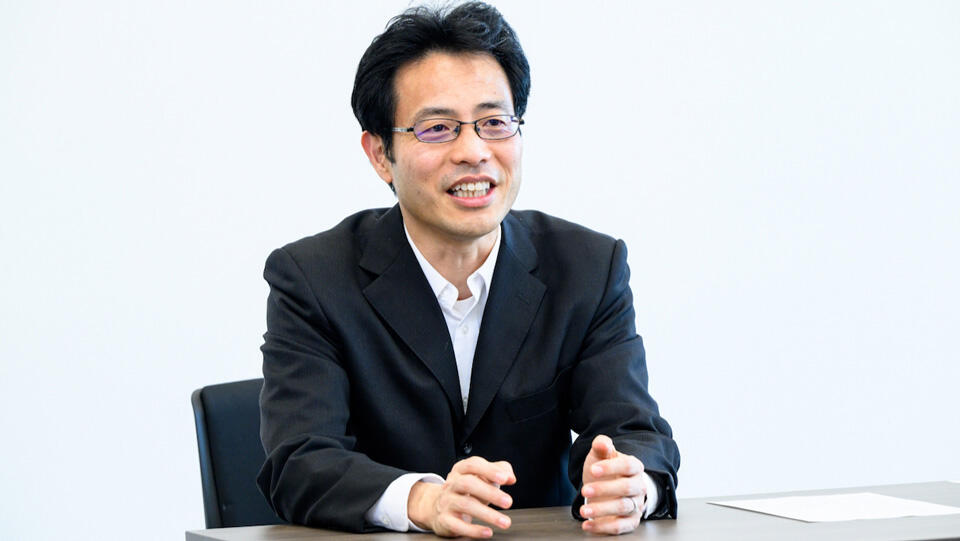
稲田 利亀:日鉄ソリューションズ(NSSOL)システム研究開発センターの稲田 利亀です。暗黙知のモデル化・定量化に向けては、アジャイル開発の手法を採り入れました。まずは熟練技術者への聞き取りで把握できた範囲で条件を設定し、それを基にシステムが作成した生産計画を熟練技術者に見てもらい、ダメな部分と、その理由を指摘してもらいながら、改良を短期間に繰り返すのです。当初は修正しても、別の部分でダメ出しが出るなどの連続でしたが、徐々に熟練技術者の計画に近い答えを出せるようになっていきました。
山本:洗い出した条件の種類は70ほどです。当初は多くても30前後だと見込んでいたのですが。今も現場の声を参考に、必要に応じて条件は継続的に見直したり追加したりしています。
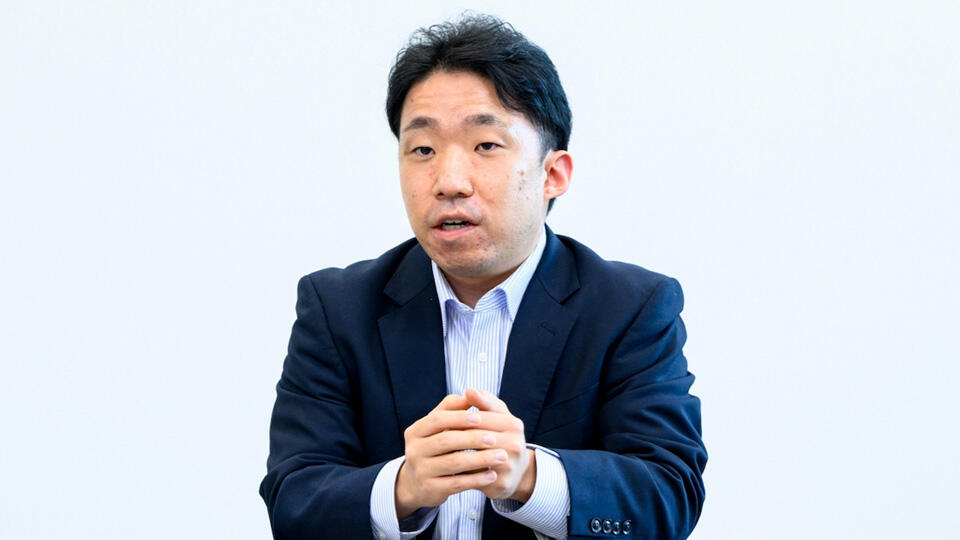
業務知見を抜きには“組合せ最適化”は困難!?
河井田:プロトタイプの数値目標として、システムで作成した生産計画をそのまま実際に利用できる割合をどれだけ引き上げられるかを定めました。使えない生産計画であれば従来通り熟練技術者が策定し直します。社内で「90日DX」と呼ぶ3カ月単位で成果を確認しながら進めるやり方で、暗黙知の抽出を繰り返したことで精度を高め、約半年で9割台にまで利用率を高められました。
森田:現場への実利用率を高めるためには、システムのレスポンスが速いことも重要です。そのために採った策の1つに「組合せ爆発をどう抑えるか」というものがあります。組合せ最適化問題では、解となる選択肢の組合せが階乗的に増加し、それに従って処理時間も天文学的な大きさとなるため、選択肢をいかに絞るかがポイントです。有効だったのは、業務知見に基づき最終的に同じ鍋にまとまりそうなスラブのグループを事前に作ることです。どんなスラブが同じグループになるのかの予測は、まさに業務ノウハウの塊ですが、グループという“縛り”を加えることで組合せの数を抜本的に減らせるようになったのです。
前久 景星:日本製鉄インテリジェントアルゴリズム研究センター 主任研究員の前久 景星です。グループの考え方も、熟練技術者の暗黙知に含まれていました。熟練技術者の暗黙知は、丁度、将棋や囲碁の世界における“定石”のようなものです。熟練技術者は、業務知見から「この条件は、そもそも考えなくていい」といった定石を活用しながら判断を下しているのです。そうした業務知見のアルゴリズムへの落とし込みは、最新技術の取り込みと同様、あるいは、それ以上に実用的なシステムを開発するうえで鍵を握る活動と言えます。
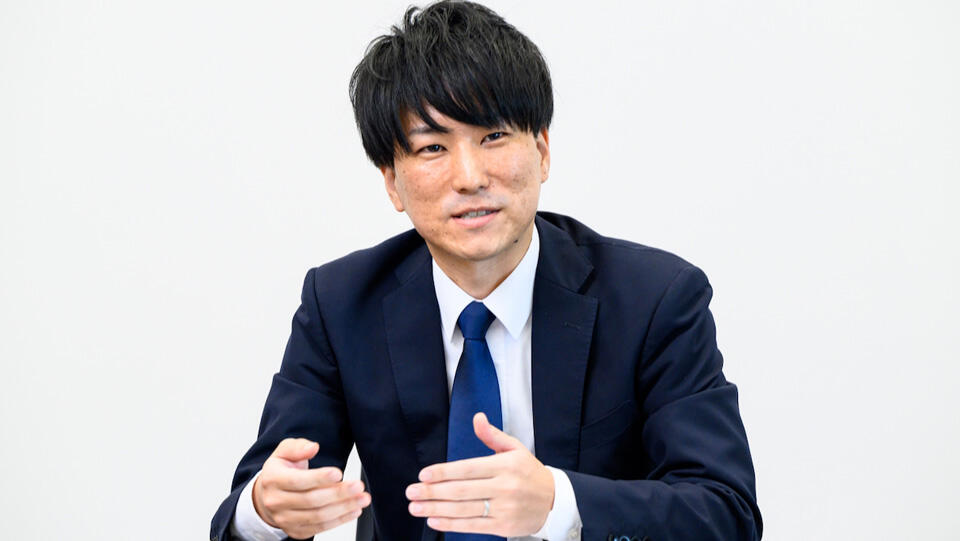
――システム化による成果を、どのように評価していますか。
河井田:生産計画の立案業務に要する時間が、従来の8時間前後から2時間程度にまで短縮できました。ただ、システム化の意義は時間の短縮の一言では到底言い表せず、当社経営における“守り”と“攻め”の双方に大きな変化を生み出し始めています。
例えば、製鋼の生産計画を立てるのは週に1度ですが、実際には、計画を一度立てれば終わりではなく、日々の進捗を確認しながら見直すことは少なくありません。ただ、生産計画は前後工程への作業指示でもあり、その生産量の大きさから一度決めた計画の見直しは、ほぼ不可能でした。それが計画時間の短縮により、これまでは時間的な制約から困難と考えられてきた前後工程も含めた生産計画の見直しが現実味を帯びてきています。
森田:システム化による時間短縮により生産計画を立案できる頻度が高まれば、計画の実行精度は当然高まり、下流工程において「どのスラブが、いつ、どれだけ届くか」をより正確に予測可能になります。その予測に対し下流工程から、各現場の生産状況を踏まえたフィードバックを受ければ、フィードバックへの対応を含めた再計算により、生産計画はより現実的なものになり、全体としての生産効率にも良い影響が期待できます。
上流工程に対しても、例えば本社が各製鉄所に生産を割り当てる前段階で製鋼の生産計画を幾度かシミュレーションすれば、製鋼工程におけるスケジュール面でのリスクの察知などにも役立てられます。
生産計画をQCD(品質、価格、納期)の指標による評価可能に
河井田:成果として特に強調したいのが“誰でも、いつでも、数分以内に”計画を立案できるようになったことです。先に説明したように製鋼の生産計画は、前後の工程への指示書でもあります。それだけに、計画立案者には、自身の計画の正しさについて、必要に応じて工場長をも説得できる能力が求められます。それ故、上流工程も下流工程も知り尽くした熟練技術者でなければ、計画立案には当たれなかったのです。
新システムでは、生産計画を評価するためにQCD(品質、価格、納期)を軸にした指標を出力できるようにもなっています。品質重視の計画だとこうで、納期を優先すればこうなるといった比較も可能です。熟練技術者の暗黙知による計画では、指標による比較はできず、計画立案者による計画の違いも“個性”といった理解に留まらざるを得ませんでした。
現在では、熟練技術者が作成した計画の評価レベルを上回る水準で、誰もが数分もかけずに立案できるまでに計画の精度も高まってきています。
――システム化で熟練技術者が不要になることには現場の抵抗も大きかったのではないですか。
河井田:実は、プロトタイプ開発の段階からプロジェクトには、熟練技術者の1人が参加していました。定年退職も視野に入る中、自身の経験や知識のすべてを残したいという本人のたっての希望によるものです。プロトタイプ当初は、自らが設計したシステムがなかなか思うような計画を作成できず、苦労も重ねたと思います。彼の存在が、暗黙知の形式知化を可能にし、計画精度も確実に高められましたし、現場へのシステム導入の推進役にもなってくれました。
他製鉄所への横展開と変化に追従し続けられる環境の実現を進める
――業務改善対象として最も影響が大きい製鋼工程のシステム化ができた今、今後は何に取り組みますか。
枚田:1つは、出鋼スケジューリングシステムの横展開です。日本製鉄では「BPM(Best Practice Model)」というコンセプトを掲げ、複数の製鉄所への同一システムの導入を進めています。従来は、製鉄所ごとに異なる設備に合わせてシステムも個別に導入してきました。今後は、システムの抽象度を高め、有効なシステムを複数の製鉄所に展開する計画です。システムの品質をより高めるために、よりきめ細かくデータを収集できる仕組みも整備していきます。
もう1つは、環境の変化に対応し続けられるシステム環境の実現です。生産する製品の変化や市況の変化などに合わせて、システムが都度の状況にフィットした計画を立案できる仕組みに変えていく必要があると考えています。当社では「精度維持管理」と呼んでいる取組みです。
森田:そのためにはNSSOLとは、これまで以上に協力体制を築く必要があります。今回のシステム構築では、プロトタイプの開発以前から、NSSOLのシステム研究開発センターの参画があってこそ実現したと言えます。今も、インテリジェントアルゴリズム研究センターへの人的支援やシステムの品質向上への支援などを受けています。
今後の精度維持管理に向けて、システム開発だけでなく、システムの運用を含めたノウハウも重要になってきます。そこでは数理最適化などの専門人材だけでなく、一般的なSE(システムエンジニア)も最適化に取り組めるように、人材育成にも期待しています。
山本:DXを実現するためのシステムは、最先端の技術だけでは成り立ちません。今回のような生産計画を立案するシステムは、現場で使いこなして業務定着を図ること自体が容易ではありません。実用レベルの計画精度を実現するには、現場の業務知見をどれだけシステムに反映できるかが鍵を握ります。加えて、システムを長く活用していくには、変化にいち早く追従し価値を提供し続けるための仕組みが必要です。精度維持管理の取組を通じ、現場とも協力しつつ、システムが最大限の効果を発揮し続けていけるよう、技術面、人材面を含めた幅広い協力関係を築いていきたいと考えています。DXの実現には、技術力と強固な協力体制の両面が不可欠です。これを実行できることがNSSOLの強みであり、使命でもあると考えています。
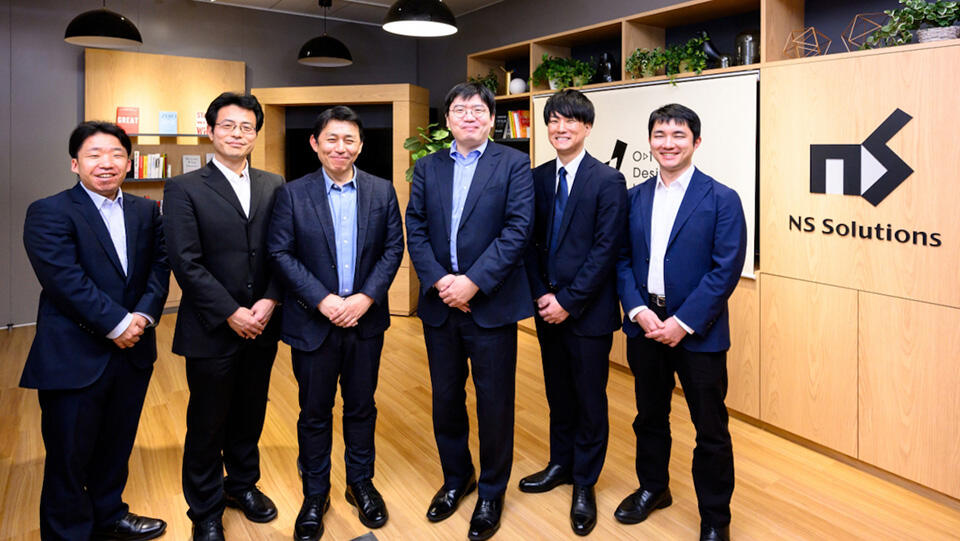